3D printer from CBS helps produce more than 500 visors for health-care personnel
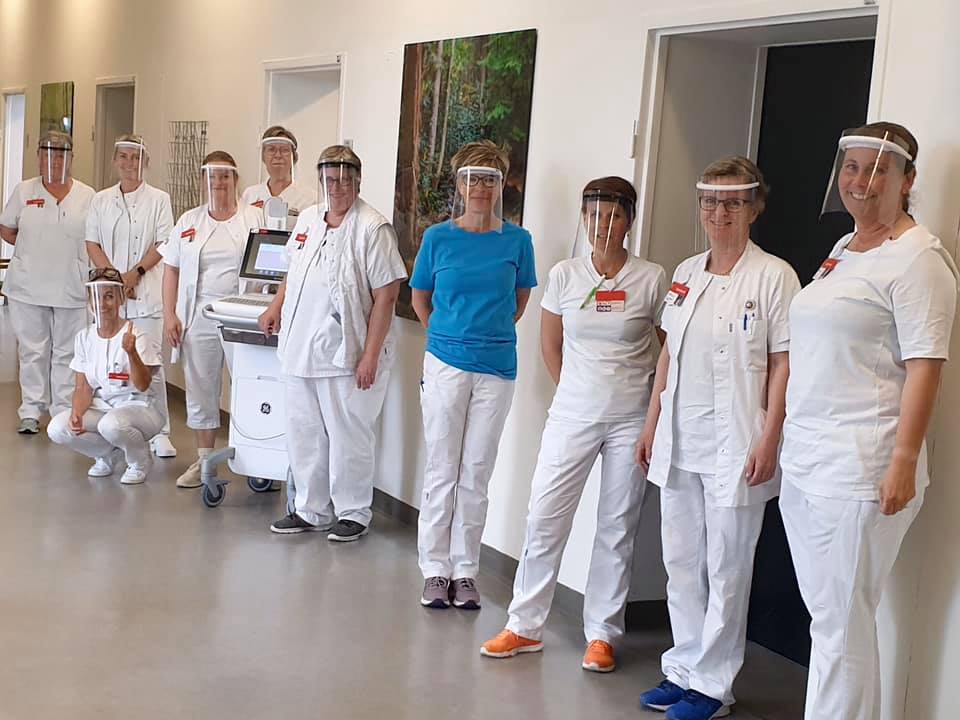
Health care personnel from Gentofte Hospital wearing 3D printed visors from DK Makers mod Corona. (Photo: DK Makers mod Corona)
A 3D printer from CBS’ BITLAB, together with more than 500 3D printers in Denmark, has helped produce 63,644 visors for Danish health-care personnel. At the peak of the corona crisis, the health-care sector “was in desperate need,” says Michael Ford Folkmann, a student and IT Advisor at CBS who picked up the 3D printer at CBS and printed the visors from home while writing his master’s thesis.
Right now, the printer is taking a break. But while the coronavirus was spreading across Denmark and sending hundreds to hospital, it was printing vital visor components for health-care personnel 24/7.
“The printer from BITLAB prints about four visors every three hour, so it wasn’t a big deal having it running. I mean, I was at home writing my master’s thesis anyway, so whenever I needed a cup of coffee, I could go and check on it,” says Michael Ford Folkmann, IT Advisor at BITLAB and graduate student at CBS.
Besides having the 3D printer from CBS, he had his company’s 3D printer, which was also kept busy printing the part of the visor that holds the plastic shield.
Michael Ford Folkmann had the idea after watching TV2’s breakfast television program ‘Go’ Morgen Danmark’ where a group from the organization DK Makers Mod Corona explained that they were printing parts for visors for the public health-care sector.
“I could print the parts for the visors myself, but I knew that BITLAB also had a 3D printer, so I called Helle Zinner, the head of the Department of Digitalization, and pitched the idea of using BITLAB’s 3D printer for the cause as well. It cost nothing, as the materials were donated to the project through DK Makers mod Corona,” he says and continues:
“And they gave me the green light to go and pick up the printer and install it at home.”
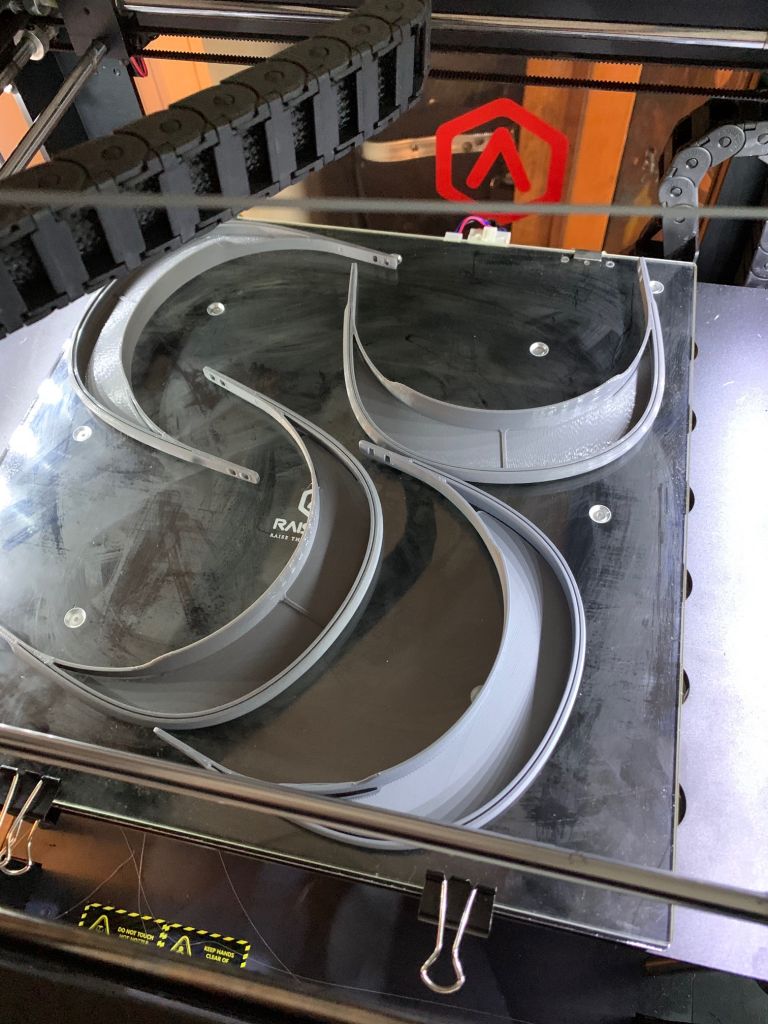
BITLAB’s printer can print four visor components at the time. (Photo: DK Makers mod Corona)
In total, the printer from CBS has made 500 parts for visors, which have been donated to the Capital Region of Denmark and further distributed to, for example, Gentofte Hospital’s Cardiology unit.
Not only has CBS helped to print visors, Michael Ford Folkmann explains that BITLAB had about 30 kilograms of unused filament, which is the material 3D printers use for printing. As the filament did not fit the newer 3D printer at BITLAB, it was donated to DK Makers Mod Corona, which sent it to people who had the machines to match. In total, with help from CBS and more than 500 volunteers’ 3D printers, DK Makers Mod Corona has produced 63,644 visor components, according to Michael Ford Folkmann.
“From what I know, the 30 kilograms of filament CBS donated have been turned into more than 1,000 visor components” he says and continues:
“Being able to provide help in a crisis is great. I have family members who work in the health-care sector, and I have heard about the problems, so it’s just brilliant to help them out.”
A state of emergency
Michael Ford Folkmann was sure that the Department of Digitalization and CBS would allow him to take home BITLAB’s 3D printer. At that time, every organization and company in Denmark seemed interested in helping in one way or another.
“At the very beginning of the crisis, Denmark and the health sector were in a state of emergency, and people were only too happy to assist wherever they could. So I was convinced that CBS wanted to lend a hand too,” he says.
At one point, the demand for visors emptied Denmark and large parts of the EU for filament for 3D printers, explains Michael Ford Folkmann.
“DK Makers Mod Corona received donations to buy filament, which it distributed to people with printers. But during the peak, it was hard to even get filament in the EU, as everyone seemed to need this material. It was quite intense witnessing that the public sector couldn’t even get its hands on it,” he says and continues:
“I know of people who, after printing the parts for the visors and putting them together with the plastic shield and rubber band, went directly to Copenhagen University Hospital to hand them over. The doctors didn’t have time to wait and said they would clean them before use.”
Even though BITLAB’s 3D printer will soon return to its natural habitat, Michael Ford Folkmann has eyed a great learning perspective in the process to share with other students.
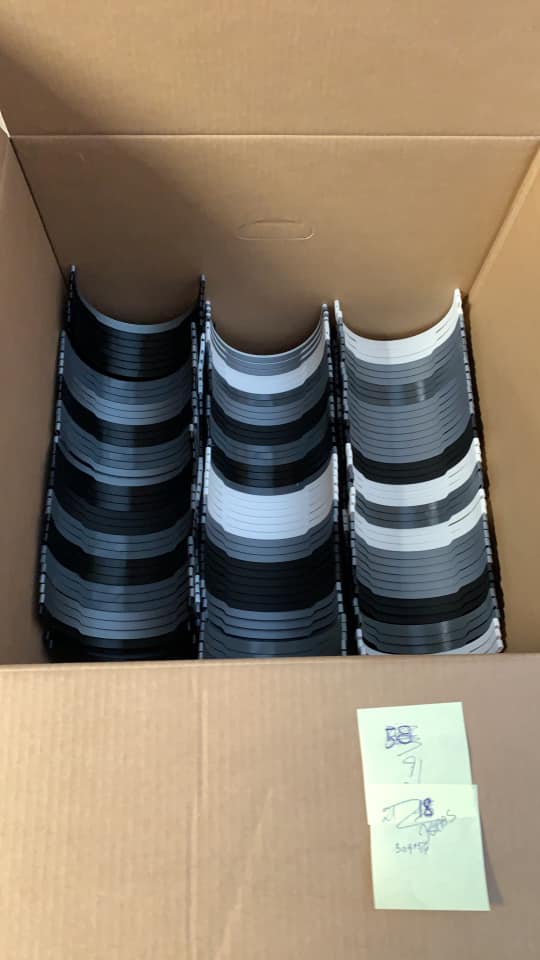
Visor components packed and ready to be sent. (Photo: DK Makers mod Corona)
“Going forwards, I can show and teach students how fast you can retool a 3D printer for a completely different purpose. LEGO also printed visor parts with an injection molding printer, but it could take up to a week or two to repurpose them for that process. With this kind of 3D printer, you can do it in a couple of hours. And that’s useful knowledge to pass on,” he says and continues:
“On BITLAB’s Facebook page we also encourage international students to seek out 3D printer communities in their home countries to print visors.”
Comments